TaeguTec Unlocks the Potential for Machining Superalloys
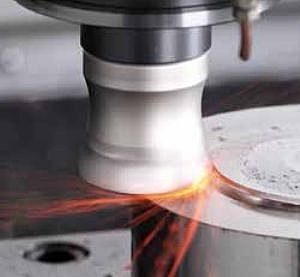
In the highly competitive world of manufacturing, the demand for increased productivity and efficiency is paramount. As manufacturers strive to push the boundaries of what's possible, the role of cutting tool technology has become increasingly crucial. One company at the forefront of this revolution is TaeguTec, a global leader in developing innovative ceramic cutting tools.
In an interview, Jae-Wook (Jay) Lee, the Milling Product Manager at TaeguTec’s world headquarters in Daegu, South Korea, discussed why ceramic cutting tools are increasingly penetrating industry sectors such as aerospace and power generation that machine HRSAs as well as the mould & die industry. As a world-leading manufacturer of high-feed milling, turning and ceramic solutions, Mr Lee discusses how TaeguTec’s cutting-edge ceramic solutions have a transformative impact on the machining of challenging materials like Inconel and other high-temperature alloys.
The Ceramic Advantage
Traditionally, machining high-temperature alloys, such as Inconel, has been a significant challenge for manufacturers. These materials are notoriously difficult to machine due to their high strength, hardness, and poor thermal conductivity. Carbide tools, the industry standard for many years, often struggle to keep up with the demands of these applications, leading to premature wear, reduced tool life, and compromised productivity.
Ceramic tooling has been in development for over 20 years, with initial applications focused on machining cast iron and hardened materials using silicon nitride ceramics. However, new ceramic grades were required as the industry moved towards machining tougher alloys like nickel-based superalloys, cobalt-based alloys, and other HRSAs. This led to the development of SiAlON ceramics, specifically engineered to address the unique challenges of machining HRSA.
The key difference between traditional silicon nitride ceramics and SiAlON is their ability to withstand the chemical reactivity and extreme heat generated during HRSA machining. Where silicon nitride tools would rapidly degrade due to early wear, SiAlON ceramics remain stable, maintaining cutting performance under intense thermal loads.
"For machining HRA and HRSA materials, like Inconel, the silicon nitride ceramic inserts we have developed are a game-changer," explains Lee. "The properties of our latest ceramic materials vastly differ from those used for machining cast iron or hardened steel. We've specifically engineered our SiAlON-based ceramics to excel in these challenging applications.”
The key advantages of TaeguTec's ceramic cutting tools lie in their ability to withstand the extreme temperatures and stresses encountered during the machining of superalloys. “Carbide tools tend to react with the workpiece material at high temperatures, leading to rapid wear despite the low cutting speed," says Lee. "Our ceramic inserts and cutting tools, on the other hand, are much more resistant to this thermal wear, allowing us to push the cutting speeds to unprecedented levels."
Boosting Productivity with Ceramic Inserts
One of the most striking benefits of TaeguTec's ceramic cutting tools is their ability to increase productivity dramatically. "We've seen cases where our ceramic inserts can achieve cutting speeds at a minimum of 20 times faster than traditional carbide tools,” Lee reveals. "This translates to a massive boost in metal removal rates and overall efficiency.”
The secret behind this performance lies in the unique design and geometry of TaeguTec's ceramic inserts. "We've developed a high-feed shape that allows us to increase both the cutting speed and the feed rate,” explains Lee. "This, combined with the inherent properties of the ceramic material, enables us to push the boundaries of what's possible in terms of productivity.”
To illustrate the point, Lee shares a case study from a leading aerospace company in Brazil. “They previously used solid carbide tools for machining Inconel 718 components, with a cutting speed of around 35m/min and a metal removal rate of just 10.5cm³/min. After switching to our ceramic inserts, they increased the cutting speed to 1000m/min and the metal removal rate (MRR) to an astounding 213cm³/min – a 20-fold improvement in productivity!”
The benefits, however, don't stop there. Lee also highlights the significant cost savings associated with TaeguTec's ceramic cutting tools. "Due to the higher feed rates and cutting speeds, our customers can achieve much greater material removal rates from a single ceramic insert compared to a carbide tool on these materials. This translates to a significant reduction in tool consumption and overall machining costs."
Overcoming the Mindset Barrier
Despite their advantages, ceramic tools have faced resistance in markets like the UK and Western Europe. Many machinists remain wary of the potential for tool breakage and short tool life. There is a deeply ingrained preference for the perceived durability of carbide tools, even though carbide struggles with high-temperature alloys and requires substantial coolant use to manage heat.
Ceramic inserts have proven themselves in global aerospace hubs and power generation sectors, delivering exceptional results. While tool life for ceramics may be limited (sometimes as little as five minutes), the incredible increase in cutting speed and productivity far outweighs the trade-off. The upside to adopting ceramic tools on HRSA materials is well proven, but engineers need to be educated on the incredible benefits and machining strategies. Increasing speeds, feeds and the MRR so dramatically can often be challenging to comprehend for engineers that have struggled to machine HRSAs for years.
Typically, a cutting tool averages 3% of the machining cost, with labour, hourly machine rates, power consumption, and business overheads absorbing the remaining 90+ %. If a ceramic insert can deliver stratospheric machining results that drastically improve the machine utilisation rate, reducing the 90+ % of machine cost whilst slightly increasing the 3% tooling cost, it doesn’t take a rocket scientist to work out the benefits of ceramic tooling. It is ‘game-changing’ for manufacturers.
For example, some aerospace manufacturers keep 50 identical ceramic tools preloaded in their machines, swapping them out rapidly to maintain continuous, high-speed production. This strategy optimises throughput more than tenfold, making the shorter tool life irrelevant. After all, the tool life is only shorter in minutes – in MRR terms, ceramic tools far exceed the performance of carbide. Ceramics also prevent the material from overheating and deforming expensive workpieces.
Despite the clear advantages of ceramic cutting tools, Lee acknowledges that some manufacturers still perceive them as too brittle and prone to breakage. "This mindset is particularly prevalent in the UK, where the aerospace industry is a major player," he says. Many companies are hesitant to switch from their tried-and-trusted carbide tools."
To address this challenge, TaeguTec has invested heavily in developing robust clamping systems and insert geometries that minimise the risk of breakage. "We've designed our ceramic inserts with a high-feed shape that not only boosts productivity but also enhances the stability and reliability of the cutting process," explains Lee.
Additionally, the company has strongly emphasised educating its customers about the true capabilities of ceramic cutting tools. "It's not just about the tool itself – it's about changing the entire machining strategy," says Lee. "We work closely with our customers to help them understand the benefits of running at higher speeds and lower depths of cut, which is the optimal approach for maximising the potential of ceramic inserts."
This educational effort has paid dividends, as Lee shares another success story from a customer in Turkey. In a recent case, a new screw-type ceramic insert—claimed to be the first of its kind globally—was tested in aerospace manufacturing. Despite initial concerns about clamping stability and heat transfer, the insert performed flawlessly in high-temperature machining trials, securing its place as a production-ready solution. "They were initially sceptical about our screw-type ceramic insert, worried that the insert or the clamping screw might break during the machining process. But after extensive testing, they were completely won over by the performance and reliability of our solution."
Expanding the Ceramic Frontier
Modern ceramic tooling isn’t just about material composition. Geometric innovation is crucial in maximising the performance of ceramic inserts. For instance, TaeguTec has introduced high-feed geometries and unique clamping designs like the screw-type inserts that further push the boundaries of what ceramics can achieve.
Not only has TaeguTec developed industry-leading ceramic grades that outperform rival products, but the company has also utilised its position as a world leader in high-feed machining to incorporate innovative cutting geometries into its series of ceramic product lines. With new high-feed insert geometries, TaeguTec can increase cutting speeds and the feed per tooth to boost material removal rates and shorten cycle times.
Furthermore, TaeguTec has expanded its ceramic ranges to include
round inserts and high-feed geometries, tailoring ceramic product lines to cover a wider array of machining scenarios. This expansion also incorporates ceramic end mills that are offered with new geometries and diameters. The latest addition to the indexable CeramicSFeed line is a range of 16, 20, and 25mm diameter tool holders with two or four insert pockets that accommodate TaeguTec’s latest BNGX 06 size inserts. The small inserts enable more insert positions per tool, subsequently permitting higher productivity.
While TaeguTec's ceramic cutting tools have already made significant inroads in the aerospace and power generation industries, the company is not resting on its laurels. "We're constantly pushing the boundaries of what's possible with ceramic technology," says Lee. One area of focus is the development of ceramic grades suitable for machining a wider range of materials, including stainless steel and titanium alloys.
"Traditionally, the use of ceramics has been limited to nickel-based superalloys due to the reactivity of silicon nitride with other materials. But we're making great strides in developing new ceramic formulations that can also handle these challenging workpiece materials." Lee is particularly excited about the potential of TaeguTec's latest ceramic product, the scroll-type insert.
TaeguTec has also developed what is claimed to be the industry’s first screw-type insert clamping system for indexable ceramic tools. "This is a true breakthrough in ceramic cutting tool design," Lee enthuses. "By incorporating a unique screw-type clamping mechanism, we've addressed the common concerns about insert breakage and clamping issues that have historically held back the adoption of ceramic tools." The screw-type insert, the first of its kind in the industry, offers several key advantages.
"Not only does it provide a secure and stable clamping solution, but it also allows us to make the cutter diameter smaller. In the end, it can replace solid carbide end mills by increasing the cutting speed and feed rate further, unlocking even greater productivity gains for our customers," explains Lee.
The Future of Ceramic Cutting Tools
As the aerospace and power generation industries continue pushing the boundaries of what's possible, the demand for cutting-edge machining solutions will only grow. Lee believes ceramic cutting tools will play a pivotal role in this evolution. "The trend in the industry is clear – manufacturers are increasingly focused on maximising productivity and efficiency while also considering the environmental impact of their operations," he says.
"Ceramic inserts are perfectly positioned to meet these demands, with their ability to deliver unparalleled metal removal rates and their inherent eco-friendliness, as they eliminate the need for copious coolant usage."
Looking ahead, Lee envisions a future where ceramic cutting tools become the norm rather than the exception in high-performance machining applications. "We're already seeing a significant shift in mindset, particularly among the more forward-thinking manufacturers willing to embrace new technologies and challenge the status quo," he says.
TaeguTec is committed to continued innovation and investment in its ceramic cutting tool portfolio to support this transition. "Whether it's developing new insert geometries, exploring alternative ceramic formulations, or enhancing our clamping systems, we're constantly striving to push the boundaries of what's possible," says Lee.
As the aerospace and power generation industries continue to demand ever-greater levels of productivity and efficiency, cutting tool technology has become increasingly critical. TaeguTec's ceramic cutting tools have emerged as a game-changing solution, allowing manufacturers to dramatically boost their metal removal rates and reduce their overall machining costs. Through a combination of innovative design, advanced material science, and a deep understanding of the unique challenges faced by its customers, TaeguTec is leading the charge in the ceramic cutting tool revolution. By overcoming the mindset barriers and demonstrating the true potential of its solutions, the company is poised to play a pivotal role in shaping the future of high-performance machining.
Ceramic cutting tools represent a paradigm shift in machining difficult materials like Inconel and other superalloys. By overcoming the traditional limitations of carbide tooling, ceramics unlock unprecedented productivity, efficiency, and sustainability. For industries focused on high-temperature applications, the future is clear—ceramic tooling is not just an alternative; it’s the next standard.
Ceramic inserts offer a pathway to enhanced performance and profitability for those ready to embrace a change in mindset, invest in modern high-speed machinery, and adopt innovative machining strategies.