Productivity Flows For Riverside
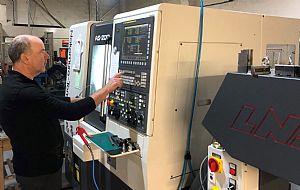
As a subcontract machine shop, Riverside Precision Engineering Ltd provides round-the-clock one-hit machining for a range of industry sectors. When the company recently noted an upturn in business, it bought not one but two Nakamura turning centres from the Engineering Technology Group (ETG).
With a range of sliding head turning centres machining components for the hydraulic, medical, brewing, valve, marine, rail and oil and gas industries, the Blackburn company was utilising an ageing Nakamura WT250 turning centre for components beyond the diameter capacity limits of its sliding head machines. To increase capacity and improve machine utilisation, the ISO: 9001:2015 certified company reviewed the market and decided to purchase a Nakamura AS200L and a Nakamura AS200 turning centre – both were delivered in November, just three weeks after ordering the machines from Wellesbourne based ETG.
Founded over 31 years ago, the 13 employee business made its first venture into CNC machining in 2002 and this was rapidly followed by volume machining on sliding head turning centres. For components beyond the diameter realms of sliding head centres, the company has a variety of fixed head single and twin-spindle turning centres. From a precision and repeatability perspective, the Nakamura WT250 has been a stand-out performer over the years. However, the reliability and utilisation of a Nakamura WT250 that is over 20 years old in a machine shop that demands maximum uptime, is something that needed addressing.
Riverside Director, Mr Scott Whalley recalls: “We have several older fixed head machines from a variety of leading manufacturers, but the Nakamura WT250 has held tolerances and repeatability better than any other down the years. We reviewed the market, and we picked the Nakamura AS200 and AS200L from ETG for a number of reasons. Firstly, we had first-hand experience of the quality, longevity and performance of the brand. Secondly, was availability. ETG had machines in stock and within 3 weeks, the two machines were on the shop floor and running. Equally important was the cost of the machines. We could have had cheaper machines on a comparative lead-time and similarly, we could have had larger machines at a lower cost. For us, it was investing in quality at a competitive cost for the long-term future of our business.”
The mix of machines was also an important factor for the manufacturer of chain and conveyor components and gas and water fittings. As Scott continues: “Components in the 50 to 65mm diameter range that are beyond our sliding head machines have been an issue. We have a lot of small-batch work typically from 50 to 500-off that is relatively simple to produce – for this we bought the Nakamura AS200 single-spindle chucking machine. For the more complex work in the 300 to 2,000+ batch range, we bought the barfed twin-spindle Nakamura AS200L. This gives us the perfect blend of capability, flexibility and capacity for our business. We have the AS200 chucker machine manually loaded with billets and the AS200L runs unmanned with a barfeed for longer batches.”
Like most subcontract manufacturers that want to maximise every inch of their floor space, Riverside is no different. “We have 19 CNC machines at present and space is at a premium. The two new Nakamura machines have fitted into the floor area of the old Nakamura WT250 – giving us two machines in the space of one. Both of the new machines are faster, more productive and can retain maximum uptime, unlike the old machine. We are now looking at replacing some of our other large ageing machines with new Nakamura machines from ETG. The beauty of the new acquisitions is that they provide very similar capacities inside the work envelope, but the machine footprint is far smaller – it's like having two machines for the price of one.”
Maximising Productivity
Despite the new Nakamura machines only being operational for a matter of weeks, the benefits are evident. As Scott continues: “The cycle times on the new Nakamura machines are much faster than our other large-capacity turning centres. In fact, the single spindle Nakamura AS200 chucking machine is faster than our ageing twin-spindle machines. The cycle times on both Nakamura machines are much faster, there is less idle time and the kinematics ensure less ‘air cutting’. The rapid rates are faster and the machines react a lot quicker than our other machines. As a business, we are extremely busy at present and our larger components up to 65mm diameter was a bottleneck. The new Nakamura machines have cut lead times from 6 weeks to just 3 weeks on these larger parts.”
Get set and go
The stability and precision of the new Nakamura AS200 and AS200L have also been a revelation for Riverside. As Scott mentions: “With our old Nakamura and some of our existing older machines, we have to take a trial cut before undertaking production - just to ensure the machine and the tools are all set correctly and there is no deviation between the machine settings and the actual parts. This is not the case with the new Nakamura AS200 and AS200L machines. The new machines are much faster to set and the probes ensure all parameters are correct, so we have 100% confidence the parts are correct every time without trial cutting or additional re-setting of parameters.”
“The guys on the shop floor really like the new machines. As well as being faster and more productive, the CNC control system has a graphic interface that is very intuitive and user friendly. Combining the new CNC interface with the simplified setting of tools in the work envelope, the team are much more confident using the new Nakamura’s.”
Cutting Costs
Still in their infancy at Riverside, it is difficult to draw direct quantifiable comparatives between the performance of the ageing turning centres and the new Nakamura machines. However, the company has instantly recognised that machine set-ups, cycle times and the throughput of orders are much improved. Similarly, the rigidity and kinematics of the new machines are apparent in improved surface finishes, tool life and the ability to ramp up machining parameters. Whilst these savings will be recognised over an extended period, one immediately evident factor of note is the energy efficiency of the new machines.
As Scott concludes: “Despite being far more productive than our older and larger machines, the new Nakamura’s draw significantly less power. We can immediately see that the machines are drawing less kVA than larger machines, and two machines are now drawing less power than one older machine. During colder periods, the heat generated by the older machines contributes to warming the factory floor – with the new Nakamura machines, the area of the shop floor where they are situated is certainly colder. This temperature drop is noticeable and it is due to the reduced power consumption, which can only be good for the environment and our operational costs.”
“Overall, we have been delighted with the service, support and training that we have received from ETG. As for the Nakamura machines, we knew we were investing in a quality brand, but now the machines are on the ground and running – the performance is making a huge difference to our business,” concludes Scott.