Motorcycle Dealership Streamlines Service Department With Nederman
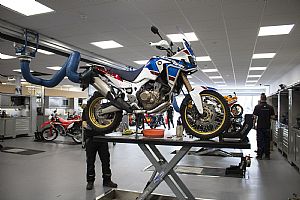
Founded in 1980, P&H Motorcycles has grown from a garden shed business to one of the largest motorcycle ‘destinations’ in the South of England. Operating from a 28,000sq/ft facility in Crawley, the growth of the business has recently noted the extension and refurbishment of its motorcycle service and repair department.
In refurbishing and enlarging the new service facility from 3,000 to 4,000sq/ft, P&H Motorcycles instigated new methodologies and a transition in working procedures to streamline its operation and improve the working environment for its staff. A central element to this refurbishment was the installation of fume extraction equipment from Nederman.
The busy service and repair centre has 14 workstations and prior to the refurbishment; P&H was using self retracting hose-reel vehicle fume extraction systems. However, the previous system had limitations that were identified by P&H Motorcycles Founder & Managing Director, Mr Paul Searle. In the first instance, the previous self retracting system would see vehicle technicians stretch the 100mm diameter retractable hoses to the motorcycle exhausts, creating a potential trip hazard. This hazard could only be overcome by installing a self retracting reel for each individual station. Secondly, the previous retracting reel configuration required a variety of specialist nozzles to be fitted to the hose-end for each and every service to ensure the extraction nozzle would cover the vehicle exhaust and deliver efficient and safe extraction.
As Mr Paul Searle recalls: “I wanted to create an efficient service department that is well equipped and will give our customers confidence in our services. I studied working practices and identified a number of areas where we could improve, fume extraction was one area. With our previous set-up, technicians using extractable hose reels for fume extraction would have to fit a nozzle cap attachment to the retractable hose reel to ensure the extraction system would envelope the bike exhaust and effectively remove workplace fume. Bikes have a variety of exhaust shapes from triangular, oval and circular through to twin-exhaust bikes. This process could be exacerbated by the sometimes difficult to access to the exhaust, created by obstacles such as fairings. Fitting the appropriate nozzle could take anything up to 15 minutes and there is always a potential risk of damaging the vehicle exhaust. This excessive and laborious task would result in one of two things; firstly, workshop inefficiency and lost time. Secondly, staff would ignore the laborious process and bike exhaust fume would enter the workshop. The refurbishment was an opportunity to address the situation and luckily we found Nederman.”
The solution suggested by Nederman was an overhead ALU150 rail with a high-volume extraction system that sits above two rows of technician bays. Hanging from the rail are four 4m self-supporting extraction arms that have rigid and lightweight internal aluminium joints. The lightweight joints can be lowered to a bike and pushed above head height with ease, avoiding trip hazards and keeping with the state-of-the-art aesthetics of the new facility. The four arms can slide along the 20m long ceiling mounted rail to the relevant technician bay and once in position, a neoprene seal on the rail will lock the position of the arm whilst in operation. During operation, each arm will generate an extraction flow rate of 200 to 250 cubic metres per hour. The ALU150 rail and the four arms are connected to a powerful high-volume centrifugal fan that extracts fume via ducting in the suspended ceiling and out of the building.
The result of the Nederman installation for the 40 employee multi-franchise motorcycle centre has been nothing short of remarkable. As Mr Searle continues: “The powerful Nederman system has extraction hoods that generate impressive suction levels. This means we no longer need nozzles, and we certainly don’t have to waste time trying to fit such nozzles. With each of our ten technicians using the Nederman system 3-4 times a day, we have calculated that we are saving £10 to £15 in labour every time each technician turns on the Nederman system. This will give us an extremely rapid pay-back period of less than 12 months.”
“Furthermore, it is easy to use, staff want to use it and we have eliminated any trip hazard whilst improving the air quality and working conditions in our service and repair department. With our previous system, we frequently had hoses wearing or becoming susceptible to heat damage from exhaust fume whilst the springs in the retractable mechanical reels would often fail. Nederman has eliminated these issues with an effective, reliable and almost maintenance-free rail system that really looks elegant and is fitting of our new facility. We have hundreds of bikes through our service and repair department every week and the easy-to-use Nederman extraction system has streamlined operations for our technicians who really like the ceiling mounted configuration.”
As part of the £130,000 workshop modernisation program, P&H Motorcycles has installed 14 service bays and with 10 technicians employed at present, the West Sussex Company has its ambitions set on further growth. Commenting on this, Mr Searle concludes: “We genuinely couldn’t be happier with the Nederman ceiling mounted system. It has generated operational efficiencies, cost savings and helped to improve throughput. Additionally, it’s a system the staff like using and it has improved extraction and workshop air quality. Furthermore, it is completely flexible. If we do employ more technicians it is very simple to add more arms to the existing rail system.”