Kerf To Unveil New Cutting Technologies at MACH
8 February 2022
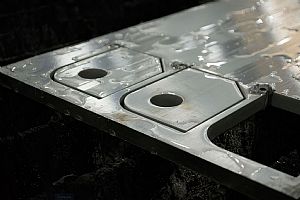
In Hall 17 on Stand 309 at MACH 2022, Kerf Developments will be returning to the UK’s showpiece manufacturing event with a multitude of impressive new technologies. As the industry leader in oxy-fuel, plasma and waterjet cutting innovations, the Rochdale manufacturer will present a dynamic mix of cost-efficient high technology cutting solutions that will undoubtedly attract visitors to its stand at the Birmingham NEC from the 4th to the 8th of April.
At MACH, Kerf Developments will be expecting its market-leading RUR2500P high definition plasma cutting machine to create a spark of attraction for show visitors. The machine with its highly acclaimed UltraSharp cutting technology has been enhanced with new advanced technologies that make this machine the choice solution for subcontract profilers, fabricators, structural steel, construction, rail and heavy engineering professionals attending MACH. This stalwart of the Kerf stable provides end-users with a unique cutting solution that combines both speed and precision with the consistently high cut quality and the lowest possible cost of manufacture. Designed and manufactured for customers with high production demand, the RUR incorporates a rigid frame design that is ultrasonically stress relieved and manufactured to highly accurate tolerances to provide remarkable performance. It is this robust build quality and precision cutting that has made the RUR2500P such a popular choice for the structural steel and heavy industry sectors. The RUR2500P has a cut width of 2m and the modular design permits table dimensions to be tailored to the demands of the end-user.
Alongside the RUR2500P, Kerf will be introducing innovations like the new Fineline 300 Plasma unit from Lincoln Electric that incorporates Advanced Piercing Technology and a new Watermist system. The new Fineline 300HD from Lincoln Electric delivers exceptional cut quality when cutting mild steel, stainless steel and aluminium whilst providing superior cut quality that minimises the need for grinding, edge preparation or other secondary operations. Specifically designed to allow full user control from a single interface, customers can rapidly change plasma current and gas pressures for better cut quality and longer consumable life. Furthermore, the FineLine 300HD features easy maintenance and a system status through the HMI. With the smallest diameter 300A torch in the industry at 38mm, the FineLine 300HD minimises secondary processing and maximise bevel and robotic cut capabilities with its new Magnum PRO LC300M torch. Working in synergy with the UltraSharp 2.0, plasma current controls are all synchronised to precisely control motion, gas flow, cut speeds and height control. This enables the technology to minimise process errors to help provide repeatable, high-quality cutting for all geometries and material thicknesses.
The FineLine 300HD also includes Advanced Process Control, an advanced piercing system that provides highly repeatable hole cutting and minimises secondary processing whilst eliminating dross from the surface to allow small holes to be cut at an optimal height. This innovation improves concentricity, cylindricity and perpendicularity of holes whilst extending consumable life and reducing piercing times. The advanced piercing system deposits dross and surface spatter through the pierced hole to provide a slag free cut surface, which eradicates the need for secondary finishing for end users.
The new FineLine 300HD also introduces a new water injection system that improves cutting performance on stainless and aluminium materials. Making the FineLine 300HD High Definition Plasma perfect for non-ferrous materials, the new watermist system further reduces dross on stainless steel and improves the cut quality on aluminium by using water as the secondary gas to control the atmosphere in the cutting zone. The result for end-users is repeatable perpendicular edges, clean and precisely finished cuts, dross, smoke, and dust reduction as well as significantly reduced running costs. By reducing the heat-affected zone, the water injection system also improves the definition of corners, reduces bevels, and delivers a lower cost per cutting metre.